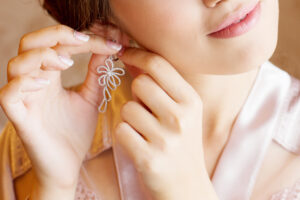
Diamonds are celebrated not only for their luster and brilliance but also for their exceptional hardness. Natural diamonds have long been the standard for cutting, drilling, and engraving due to their unmatched durability. However, the advent of artificial diamonds has introduced a new era in precision cutting and sharpening tools, taking the concept of sharpness to an entirely new level. One of the defining characteristics of diamonds is their hardness. The Mohs scale of mineral hardness rates diamonds as the hardest natural substance, with a perfect score of 10. This extraordinary hardness is a result of the unique atomic structure of diamonds, where each carbon atom is tetrahedrally bonded to four other carbon atoms, forming a three-dimensional lattice. This structure makes diamonds incredibly resistant to deformation and wear, making them the ideal choice for various cutting and abrasion applications. While natural diamonds have been cherished for their exceptional hardness and have been used in tools such as diamond saw blades and grinding wheels, the emergence of artificial diamonds has significantly expanded the possibilities of precision cutting and sharpening. Artificial diamonds, also known as synthetic diamonds or lab-grown diamonds, are engineered through high-pressure, high-temperature (HPHT) or chemical vapor deposition (CVD) processes. These controlled growth methods allow scientists to produce diamonds with specific properties, including hardness, sharpness, and durability.
The sharpness of artificial diamonds is a game-changer in various industries, most notably in the production of cutting tools. These synthetic diamonds can be precisely engineered to have the desired sharpness, edge retention, and cutting efficiency, making them indispensable in applications where precision and durability are crucial. Industries such as manufacturing, aerospace, healthcare, and electronics have embraced the superior cutting abilities of artificial diamonds. In the field of healthcare, for instance, artificial diamonds have revolutionized surgical instruments. Scalpel blades made with synthetic diamonds are renowned for their unparalleled sharpness and precision, reducing tissue damage, pain, and recovery time for patients. These advanced cutting tools are particularly beneficial in delicate surgical procedures, such as eye surgery and microsurgery. The electronics industry relies on artificial diamonds to manufacture cutting-edge technologies. Synthetic diamond wafers are used in the production of high-quality semiconductors. The sharpness and precision of artificial diamonds enable the precise dicing and cutting of silicon wafers, contributing to the creation of smaller, more powerful, and energy-efficient electronic devices. Another application where artificial diamonds shine is in the field of gemstone cutting and polishing. Synthetic diamond cutting tools can delicately shape and facet gemstones with remarkable precision, preserving the maximum carat weight while minimizing material loss. This level of precision is especially valued in the jewelry industry, where every facet and contour must meet exacting standards.
In conclusion, artificial diamonds have ushered in a new era of precision cutting and sharpening tools. Their remarkable hardness, engineered sharpness, and durability have expanded the boundaries of what is possible in various industries, from healthcare to electronics to gemstone cutting. The adoption of artificial diamonds has not only enhanced efficiency but has also revolutionized the way we approach precision cutting, offering benefits that extend across multiple sectors.